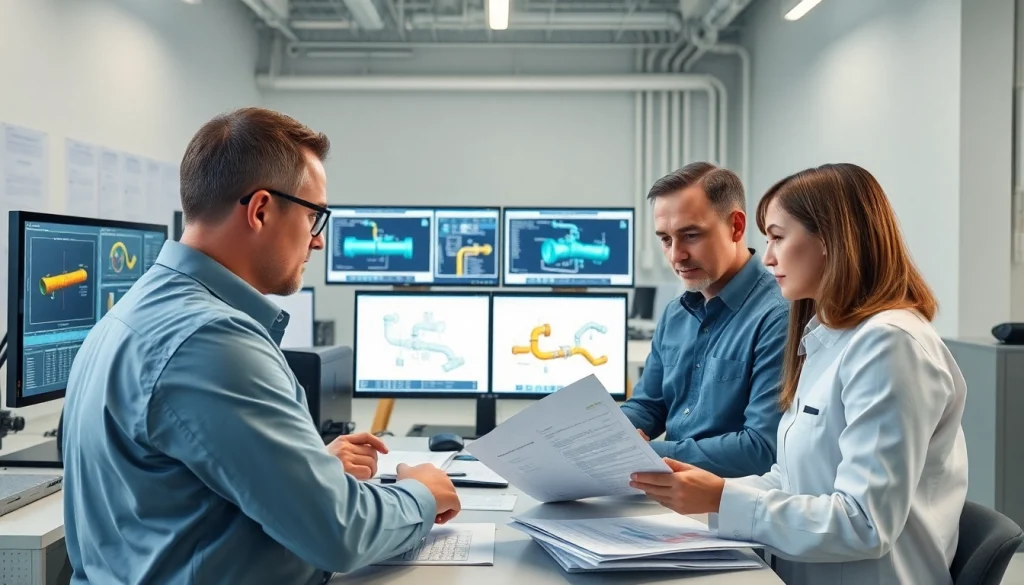
Understanding Piping Stress Analysis and Its Importance
Piping systems play a critical role in various industries, from oil and gas to chemical processing and manufacturing. The engineering discipline known as piping stress analysis examines how these systems react to different internal and external forces, ensuring operational safety and efficiency. A specialized piping stress analysis company provides essential insights and evaluations that prevent structural failures and promote the longevity of piping systems.
What is Piping Stress Analysis?
Piping stress analysis involves evaluating the load-bearing capacity of piping systems. It assesses how pipes behave under various conditions such as temperature fluctuations, pressure changes, and mechanical loads. This analysis is vital for identifying potential weaknesses and optimizing the design to mitigate risks associated with pipe failure. Furthermore, the analysis encompasses the study of flexibility, which pertains to how pipes adapt to changes in size, shape, and length due to environmental factors.
The Role of a Piping Stress Analysis Company
A piping stress analysis company specializes in conducting thorough evaluations of piping systems, employing both modeling techniques and software to deliver accurate results. These companies often utilize industry-standard tools such as CAESAR II and ANSYS to simulate real-world conditions. Their primary goal is to ensure compliance with engineering standards and regulations while delivering safe and efficient designs for their clients.
Key Benefits of Proper Stress Analysis
- Enhanced Safety: Identifying weak points reduces the risk of catastrophic failures, protecting both personnel and infrastructure.
- Cost Efficiency: Preventive analysis can help avoid expensive repairs and downtime caused by unexpected pipe failures.
- Regulatory Compliance: Adherence to industry codes and standards, such as ASME B31, is critical for operational legality.
- Informed Decision-Making: Detailed insights guide engineers and project managers in strategically planning future projects and modifications.
Techniques and Tools Used in Piping Stress Analysis
Common Software and Modeling Techniques
Modern piping stress analysis relies heavily on advanced software technologies that allow for sophisticated modeling and simulations. Some widely utilized software programs include:
- CAESAR II: A leading tool for pipe stress analysis that provides comprehensive evaluation capabilities for both static and dynamic loads.
- ANSYS: Renowned for its finite element analysis (FEA) capabilities, useful in assessing material response to various stresses.
- AutoPIPE: This software specializes in automatic calculations for verification of pipe stress analysis, ensuring compliance with necessary codes.
- SolidWorks: While primarily a 3D CAD software, it can be used in conjunction with other stress analysis tools for structural assessments.
Manual vs. Automated Analysis: Pros and Cons
While automated tools significantly enhance efficiency and accuracy, understanding manual analysis techniques is crucial for engineers:
- Manual Analysis: Provides deeper insights into the calculations, allowing seasoned engineers to detect subtle issues but can be time-consuming.
- Automated Analysis: Increases speed and decreases the likelihood of human error, although it may sometimes overlook less evident problems that could arise from unique configurations.
Latest Trends in Piping Stress Analysis Technologies
The field of piping stress analysis continues to evolve with advancements in technology. Some emerging trends include:
- Artificial Intelligence: AI is increasingly being integrated into stress analysis tools to enhance predictive capabilities and risk assessments.
- Cloud Computing: Cloud-based software allows for remote collaboration and real-time data sharing among project teams, streamlining communication and efficiency.
- Virtual Reality: VR technologies are used for visualizing complex piping systems in 3D, facilitating better understanding and design decisions.
Best Practices for Effective Piping Stress Analysis
How to Choose the Right Analysis Parameters
Selecting appropriate parameters is a prerequisite for conducting effective piping stress analysis. Engineers should consider factors such as:
- The type of fluid being transported, as this influences pressure and temperature conditions.
- The materials used in piping, which directly affects flexibility and load-bearing capacity.
- The environmental factors, such as temperature variations and seismic activity, especially for installations in high-risk areas.
Importance of Compliance with Industry Standards
Compliance with industry standards such as ASME, ISO, and API is paramount for any piping stress analysis project. These guidelines ensure that designs are safe, reliable, and efficient, further minimizing the risk of failure. Regular audits and adherence to these regulations during the engineering process are key components for maintaining integrity and customer trust.
Collaboration with Other Engineering Disciplines
Piping stress analysis does not occur in isolation; it requires collaboration with various engineering fields such as structural, mechanical, and civil engineering. This intersection fosters comprehensive analysis and innovative solutions, resulting in enhanced project outcomes. Engineers should establish open lines of communication throughout the project lifecycle to address interdisciplinary challenges and share insights effectively.
Challenges Faced in Piping Stress Analysis
Common Issues in Stress Analysis Execution
Piping stress analysis can be fraught with challenges, including:
- Inaccurate Input Data: Relying on outdated or incorrect data can lead to flawed analysis results. Regular updates and validation of input parameters are essential.
- Complex Geometry: Unconventional piping layouts or extensive systems can pose difficulties during analysis, requiring specialized expertise.
- Timer Constraints: Tight project timelines can pressure teams, often leading to oversight or rushed calculations.
Mitigation Strategies for Analysis Errors
To mitigate potential errors in piping stress analysis, consider implementing these strategies:
- Regular training and updates for engineering teams to remain current with industry standards and technologies.
- Developing a quality assurance process that includes peer reviews of analyses to catch errors before finalization.
- Utilizing modular software that enables efficient testing of complex designs, providing faster real-time feedback.
Addressing Client Concerns in Analysis Reports
Clients often have legitimate concerns regarding the reliability and comprehensiveness of analysis reports. To address these concerns:
- Provide clear explanations of methodologies and assumptions made during the analysis.
- Outline potential risks alongside recommended mitigation strategies to foster confidence in decision-making.
- Engage in regular updates and discussions throughout the project to maintain transparency and trust.
Case Studies: Successful Projects by Piping Stress Analysis Companies
Highlighting Notable Projects and Their Outcomes
Several piping stress analysis companies have successfully executed notable projects that demonstrate the value of their services:
- Oil Processing Facility: A major company engaged in oil extraction expanded its processing facility in a seismically active region. Through comprehensive piping stress analysis, the design integrated flexibility to accommodate seismic movements, successfully passing governmental inspections and ensuring operational safety.
- Chemical Plant Revamp: A chemical manufacturing plant underwent significant gear replacements that altered piping configurations. A meticulous stress analysis identified high-stress points, leading to the adoption of reinforced materials that improved the system’s durability, subsequently avoiding costly downtimes.
Lessons Learned from Complex Projects
Complex projects often reveal valuable lessons, including the importance of:
- Thorough upfront analyses to anticipate challenges, especially those stemming from environmental pressures.
- Continuous collaboration and communication among interdisciplinary teams to facilitate insights and innovative solutions.
- Revisiting designs periodically to ensure robustness aligns with the latest technology and safety standards.
The Future of Piping Stress Analysis in Engineering
The future of piping stress analysis holds promising advancements. As technologies continue to develop, we can expect:
- Greater reliance on automation and AI which will improve prediction capabilities and streamline workflows.
- Increased adaptation of remote monitoring technologies, allowing for ongoing evaluation that can preemptively address issues before they culminate in failures.
- Heightened emphasis on sustainability, which will push engineers to design systems that minimize environmental impact while maximizing efficiency.