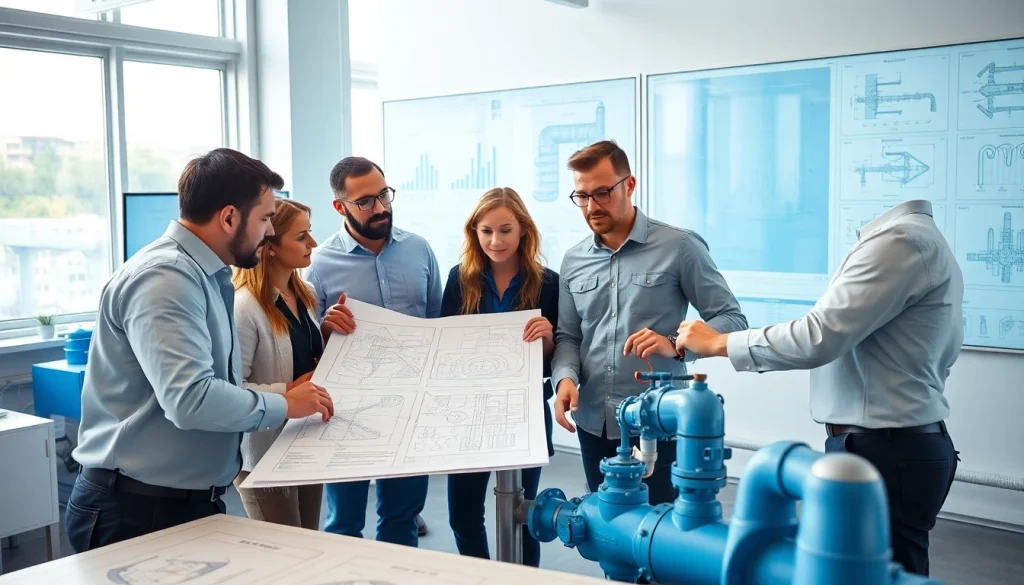
Understanding Piping Stress Analysis and Its Importance
Piping stress analysis is a critical component of engineering and design in various industries, ensuring that the piping systems can withstand operational loads without failure. As a piping stress Analysis Company, we emphasize the significance of thorough analysis in designing safe, efficient, and reliable systems that not only meet operational demands but also adhere to regulatory standards.
What is Piping Stress Analysis?
Piping stress analysis entails evaluating the stresses experienced by piping systems under operational conditions. It focuses on the impact of thermal expansion, pressure changes, and mechanical loads on pipe configurations to ensure structural integrity. By simulating real-world conditions, engineers identify potential weak points and design flaws before physical systems are constructed.
Why Piping Stress Analysis Matters
The importance of piping stress analysis cannot be overstated. This process goes beyond ensuring that pipes are physically capable of handling the necessary loads; it also plays a crucial role in safety and efficiency. Proper analysis helps in:
- Preventing Failures: Identifying stress concentrations can prevent costly failures or disasters during operation.
- Optimizing Designs: Engineers can design piping layouts that are not only functional but also cost-effective and materials-efficient.
- Meeting Regulatory Requirements: Compliance with industry codes and regulations is critical. Stress analysis documentation satisfies these standards.
Common Applications Across Industries
Piping stress analysis has wide-ranging applications across several sectors including:
- Oil and Gas: For transporting crude oil and natural gas, ensuring the pipelines operate under extreme conditions without failure is vital.
- Power Generation: In power plants, piping systems carry steam, water, and other fluids under high pressure and temperature.
- Aerospace: Piping analysis ensures safety in systems that manage fuels and fluids in aircraft.
- Manufacturing: Many manufacturing processes require precise fluid management, where stress analysis safeguards equipment.
Key Techniques and Tools in Piping Stress Analysis
Essential Software and Technology
Advancements in technology have transformed how piping stress analysis is conducted. Modern engineers rely on specialized software such as CAESAR II, ANSYS, and AutoPIPE to perform detailed simulations. These tools enable engineers to:
- Model complex piping systems with high accuracy.
- Perform real-time analysis under various load conditions.
- Generate comprehensive reports that assist in decision-making.
Manual Calculations vs. Automated Solutions
While manual calculations have traditionally been used for piping stress analysis, the complexity of modern systems often necessitates automated solutions. Automated software allows for efficiency and accuracy that manual methods may struggle to achieve. However, understanding the fundamentals of manual calculations is still essential for engineers to verify automated outputs and ensure that no critical factors are overlooked.
Best Practices for Accurate Analysis
To achieve the most reliable results from piping stress analysis, consider these best practices:
- Data Accuracy: Ensure input data regarding material properties and operational conditions are precise.
- Comprehensive Modeling: Incorporate all components of the piping system, including supports, restraints, and attachments.
- Iterative Testing: Regularly test and revise models based on new data or conditions.
Common Challenges Faced During Piping Stress Analysis
Identifying Design Limitations
One of the first challenges in piping stress analysis is pinpointing design limitations. Oftentimes, designs have inherent weaknesses that may only manifest under specific conditions. Engineers must be vigilant and conduct stringent reviews throughout the design process.
Addressing Material Fatigue and Failure
Material fatigue can lead to catastrophic failures if not adequately addressed during the analysis stage. Understanding the properties of materials used in the piping system, particularly under varying temperatures and pressures, is crucial. Regular inspection and analysis can help foresee potential fatigue issues.
Keeping Up with Regulatory Standards
Regulatory compliance can be a monumental task for engineers. Different industries and geographic locations have unique requirements. Thus, remaining current with changes in regulations and ensuring that all analyses comply with these is vital for legal and operational integrity. Working closely with regulatory agencies during design can mitigate compliance issues during implementation.
Case Studies: Successful Piping Stress Analysis Implementations
Oil and Gas Sector Insights
A notable case study comes from an offshore oil platform where piping systems are subjected to extreme environmental conditions. A thorough stress analysis revealed critical stress points in the design, leading to a redesign that ensured the longevity and safety of the system. Predictive maintenance was also established to address potential wear before it became critical.
Power Generation Case Examples
In one power generation facility, extensive piping stress analysis identified issues with thermal expansion that could have resulted in leaks and failures. By adapting the design based on analysis results, the facility improved its overall efficiency, which led to significant cost savings in operations.
Innovations in Industrial Settings
A manufacturing plant utilizing automated piping systems implemented advanced stress analysis software to streamline operations. The ability to visualize stress distribution in real time allowed for proactive adjustments, limiting downtime and ensuring optimal production outputs.
Future Trends in Piping Stress Analysis
Integrated Digital Solutions
The future of piping stress analysis lies in further integration of digital technologies. Advanced data analytics, AI, and real-time monitoring systems will likely redefine how stress analysis is conducted. These solutions promise to deliver greater accuracy while predicting failures before they happen.
Sustainable Practices and Material Innovations
As industries shift toward more sustainable practices, the demand for innovative materials that can withstand harsh environments while minimizing environmental impact is rising. Future piping systems will increasingly utilize composites and advanced alloys requiring new analysis approaches.
Preparing for Advanced Engineering Challenges
With the advent of smart city initiatives and automated systems, engineers must prepare for increasingly complex designs. This shift requires adaptive skills and knowledge in the latest software and analytical techniques to ensure safety and functionality.