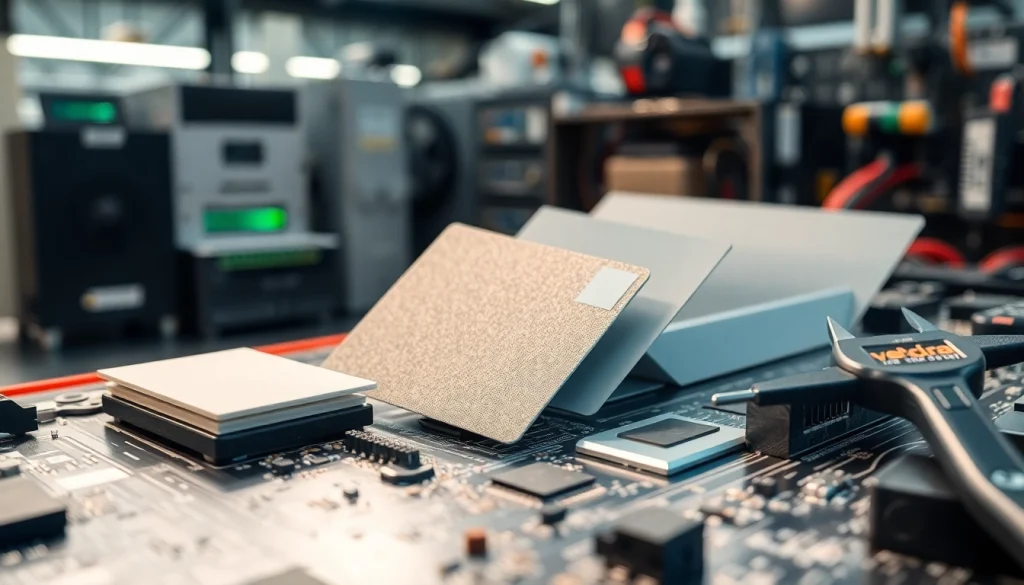
1. Introduction to Thermal Management Materials
In today’s fast-paced technological landscape, effective thermal control is a critical aspect of electronic design and manufacturing. Thermal management materials are integral components in electronics, ensuring performance reliability and extending the lifespan of devices by effectively dissipating heat generated during operation. These materials include a wide variety of products designed to manage thermal energy, making them essential in various industries such as consumer electronics, automotive, aerospace, and more. Thermal management materials serve not only to protect delicate components from overheating but also to enhance overall system performance.
1.1 Definition and Importance of Thermal Management Materials
Thermal management materials can be defined as substances used to provide thermal interface solutions between heat-generating components and heat sinks or other cooling devices. They play a vital role in optimizing thermal conductivity and minimizing thermal resistance, thus facilitating efficient heat transfer. Without proper thermal management, electronic components can suffer from overheating, leading to performance degradation, operational failure, or even complete device failure.
1.2 Key Applications Across Industries
Thermal management materials are utilized extensively across various sectors. In the consumer electronics industry, they are crucial for smartphones, laptops, and tablets, where compact form factors generate significant heat. In automotive applications, these materials are essential for managing the thermal profile of batteries, power electronics, and internal combustion engines. Aerospace applications also leverage advanced thermal materials to deal with extreme temperature variations and ensure the reliability of avionics systems.
1.3 Common Challenges in Thermal Management
Despite the advancements in thermal management, several challenges remain. High power densities in modern electronics can cause localized hot spots, making it difficult to achieve uniform temperature distributions. The integration of diverse materials can also lead to thermal interfaces with varying properties, complicating thermal solutions. Furthermore, the ongoing trend towards miniaturization necessitates that thermal materials maintain high performance in increasingly constrained spaces.
2. Types of Thermal Management Materials
Understanding the various types of thermal management materials is essential for selecting the right solution for a specific application. Each material type offers unique properties and benefits, making them suitable for different challenges.
2.1 Thermal Interface Materials (TIMs)
Thermal Interface Materials (TIMs) are essential for enhancing the thermal transfer between surfaces, such as between a semiconductor device and a heat sink. These materials can be categorized into several types, including thermal pastes, thermal adhesives, and reinforced films. Their primary function is to fill microscopic gaps between surfaces to create a more effective thermal pathway. For instance, thermal pastes are often used in computer processors to reduce thermal resistance, while thermal adhesives are employed in applications requiring bond strength along with heat conduction.
2.2 Thermal Pads and Gap Fillers
Thermal pads and gap fillers are commonly used as a quick and effective means of ensuring proper thermal contact between components. Typically made from silicone or other compliant materials, they can conform to the surfaces of electronic devices and accommodate irregularities. Gap fillers are particularly advantageous in applications where traditional TIMs may not suffice due to large separation gaps or mechanical stress. They provide significant thermal conductivity paired with excellent insulation properties, making them suitable for automotive and industrial systems.
2.3 Thermal Gels and Phase Change Materials
Thermal gels are viscoelastic materials that are particularly effective in situations where high thermal conductivity and flexibility are required. They are commonly found in high-performance computing devices and LED technologies. Phase Change Materials (PCMs), on the other hand, exhibit unique behavior by absorbing or releasing heat when they change states (from solid to liquid and vice versa). This unique property allows PCMs to maintain stable temperatures for prolonged periods, making them ideal for applications in thermal batteries and energy storage systems.
3. Benefits of Using Thermal Management Materials
The implementation of thermal management materials yields numerous advantages, significantly impacting the performance and longevity of electronic systems.
3.1 Enhanced Heat Dissipation and Cooling Efficiency
One of the primary benefits of thermal management materials is their ability to enhance heat dissipation and cooling efficiency. By facilitating better thermal transfer, these materials help keep electronic components operating within safe temperature ranges, thus preventing potential thermal overloads and improving overall system efficiency.
3.2 Improved Product Reliability and Longevity
Electronics often face thermal cycling, leading to fatigue and early failure if not managed properly. The use of appropriate thermal management solutions can significantly improve product reliability and longevity, as they prevent overheating and associated damage. This results in reduced warranty claims and lower overall operational costs.
3.3 Cost-Effectiveness in Thermal Management
Investing in high-quality thermal management materials may appear costly upfront, but the long-term savings due to reduced failures, maintenance costs, and extended product lifespan are substantial. Companies that prioritize effective thermal solutions often find that their products are more competitive in the marketplace due to enhanced performance and reliability.
4. Best Practices for Implementing Thermal Management Materials
When integrating thermal management materials into design processes, adhering to best practices can optimize performance and ensure effectiveness.
4.1 Selecting the Right Material for Your Application
The selection process for thermal management materials should involve a thorough understanding of the specific thermal requirements for your application. Factors to consider include the thermal conductivity required, environmental conditions (such as temperature fluctuations), and mechanical stresses. Engaging with suppliers or manufacturers for technical data sheets can provide insight into which products will best suit your needs.
4.2 Proper Installation Techniques
Even the best thermal management materials will underperform if they are improperly installed. Following manufacturer guidelines regarding the application thickness, surface preparation, and curing times is crucial. Additionally, ensuring adequate contact pressure and alignment can significantly enhance thermal performance.
4.3 Performance Monitoring and Assessment
Ongoing evaluation of thermal management strategies is vital. Employing thermal imaging and other monitoring techniques can allow for real-time assessment of temperature profiles and thermal performance. Identifying and addressing thermal issues promptly can help mitigate larger problems down the road, ensuring both short-term and long-term reliability.
5. Future Trends in Thermal Management Materials
The landscape of thermal management materials is continually evolving, with trends towards improved performance, greater sustainability, and more innovative applications.
5.1 Innovations in Material Science
Ongoing research in materials science is yielding innovations in thermal management that enhance performance characteristics significantly. Advanced nanomaterials and composites are being developed to provide not just higher thermal conductivities but also lighter weights and greater mechanical flexibility. For instance, graphene and carbon nanotube-based solutions are showing great promise in providing exceptional thermal management capabilities.
5.2 Sustainability and Eco-friendly Solutions
As environmental consciousness grows, the push for sustainable thermal management materials has increased. Manufacturers are exploring the use of bio-based materials and recyclable composites that align with eco-friendly practices while still delivering the necessary thermal performance. This trend is particularly vital in sectors like automotive and consumer electronics, where sustainability regulations are tightening.
5.3 Predictive Maintenance and IoT Integration
The integration of IoT technology with thermal management systems offers advanced capabilities for predictive maintenance. Sensors embedded in thermal materials can monitor temperature changes and provide actionable insights, allowing for timely interventions before failures occur. This proactive approach can significantly enhance operational reliability and extend equipment lifespan.